Gensler‘s Martina Parrish shares how design and material standards can transform sustainability efforts.
According to Scientific American, 2024 was the hottest year on record; the first to exceed 1.5 degrees Celsius above preindustrial temperatures. If this trend continues, we’ll run out of time to limit warming to under 1.5 degrees set by the Paris climate accord.
In an average building today, operating energy accounts for 72% of the overall energy consumption. Strategies for reducing operating carbon include right-sizing, significantly reducing operating energy per square foot, gradually increasing onsite renewable energy production, and increasing flexibility for renewable procurement through electrification.
Additionally, as the world’s population continues to grow, the amount of building floor space needed is expected to double between now and 2060—equivalent to building New York City every month for 40 years. While operational carbon emissions rates can be reduced over time through efficiency upgrades and grid decarbonization, embodied carbon is an up-front environmental impact. Opportunities for reducing embodied carbon as quickly as possible need to be identified in order to eliminate emissions associated with construction growth.
Making a Difference through Measured Sustainability Standards
Because Gensler’s reach into the built environment is vast, it is in the position to be leaders in the shift toward environmentally responsible material sourcing.
A critical step in this process is setting sustainability standards for the products specified daily on behalf of clients. These specifications are included in the Gensler Product Sustainability (GPS) Standards. The GPS Standards establish sustainability performance criteria for the top 12 most commonly used, high-impact, product categories selected for our projects.
They are also based on the carbon impact of a products’ materials and manufacturing processes, the volume at which we specify each product category, and market readiness to demonstrate sustainability (through EPDs, third-party certification programs, and VOC emissions testing data).
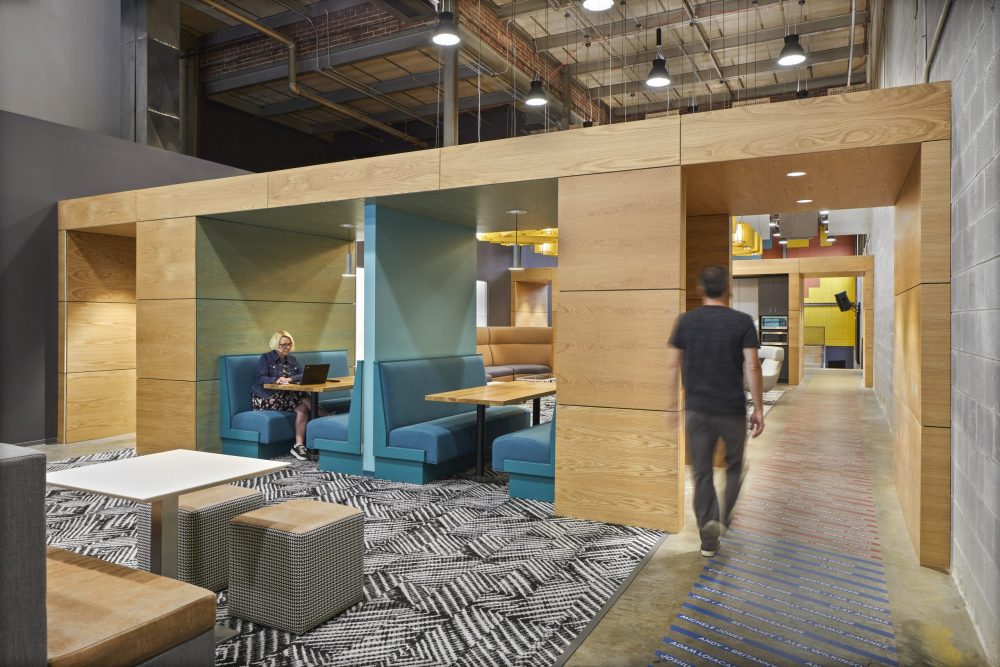
Most clients don’t have time to dive into every detail of material sourcing, but they want to make good decisions—ones that are healthier, smarter, and cost-effective. This is where the GPS Standards come in—to take the guesswork out of choosing better materials, making it easier to reduce pollution, waste, and unnecessary costs.
Instead of using complex sustainability terminology, GPS helps people make choices that work for them—without extra stress or cost by doing the following:
- Cuts down waste and saves money – materials last longer, so clients don’t have to replace them as often. That means less spending, less waste, and less hassle down the road.
- Creates cleaner, healthier spaces – Many building materials release chemicals into the air. The standards prioritize products that don’t pollute indoor spaces, helping people breathe easier.
- Reduces pollution without sacrificing quality – Swapping even one high-impact product for a better GPS-approved option can significantly lower a building’s environmental footprint.
- Helps clients stay ahead of the game – Building standards and expectations are getting stricter. Approved materials help clients avoid last-minute compliance issues and future-proof their spaces.
As GPS is more commonly used on projects across the globe, we are understanding the impact it has. Partnerships with manufacturers reaching out to be added to our list of products has increased, and we’re sharing project case studies that demonstrate how GPS informs the design process for specific projects.
Putting the Criteria to Work
According to the Allergy & Asthma Network, The average person spends up to up to 90% of their day inside. For many people, that time may be spent at an indoor workplace.
There are numerous ways that the built environment can create a healthy workspace.
Occupants of green certified buildings report better cognitive function and less mental and physical health symptoms.
Findings from the International Journal of Building Science support this argument.
GPS helps our clients streamline the materials selection process to achieve a healthier outcome. GPS also helps set a framework in the building infrastructure so the workplace can be complemented by other factors such as optimal lighting, acoustics and biophilic design.
Workers who feel valued, safe and healthy in their workplace can reduce insurance costs and increase productivity, satisfaction, and retention.
To drive sustainable development through GPS standards is to prove that it is possible. Our design team is working with Savills on its new workspace in Uptown Dallas. Additionally, our work with Jackson Walker in Houston is another example of how we collaborate with the client to meet these standards. From the start of the schematic design (SD) phase, our team ensured that every finish presented was on the approved list required to meet GPS criteria.
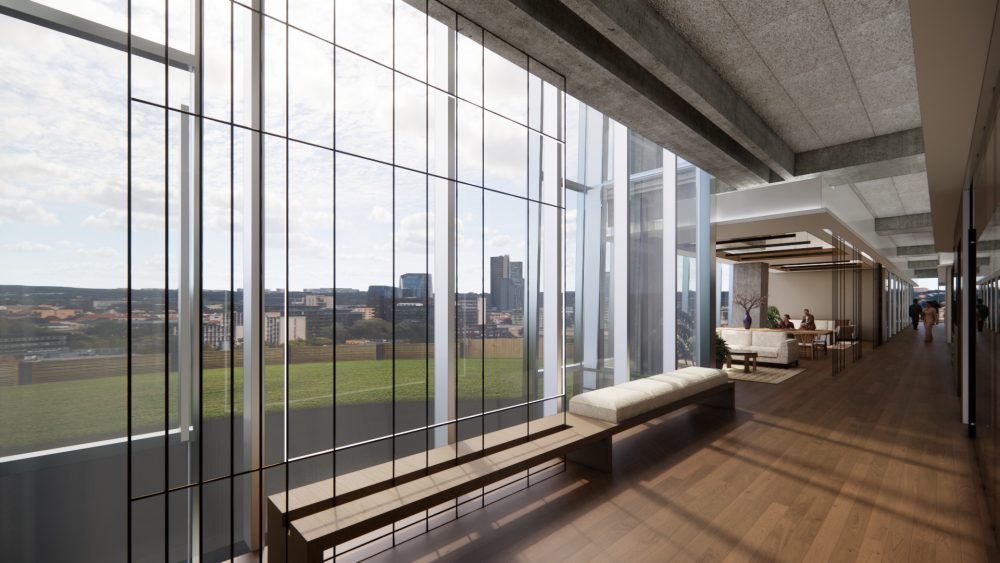
Both project examples demonstrate how our teams are effectively implementing GPS standards, and showing our clients, the meaningful and beneficial results of making a positive difference in selecting products and materials.
Looking Ahead
If we genuinely want to make a positive impact on the human experience, and prepare for a resilient future, it’s imperative that we help our clients reach their carbon targets and our goal of making every building in our portfolio net zero carbon.

Additionally, economic benefits from healthy buildings can be divided into three categories: higher rents and property values, operational costs savings, and health savings from reduced sick leaves.
Research from the International WELL Building Institute (IWBI) shows that adopting healthy building practices can yield the following benefits:
- $200 billion in annual productivity gains from reducing Sick Building Syndrome symptoms by 20% to 50%.
- $38 billion in annual economic benefits from increasing ventilation rates in U.S. offices.
- A return of $3.48 per dollar spent on workplace wellness programs due to reduced medical costs and an additional $5.82 from decreased absenteeism.
- Up to 101% improvement in cognitive function, translating to employee productivity gains of $6,500 to $7,500 per person annually.
- A net present value of $115 per square foot over 10 years in high-performing buildings, driven by better retention and well-being.
Reducing carbon footprint cuts emissions by minimizing the amount of greenhouse gases released into the atmosphere during its construction, operation, and end-of-life stages, primarily achieved through energy efficiency measures like better insulation, renewable energy sources, and selecting low-carbon building materials, thereby lowering the building’s overall energy consumption and associated emissions. GPS is helping designers to select low-carbon building materials.
When executed through proper planning, and accountability, strategic climate action plans can produce tangible results toward climate goals so organizations can achieve sustainability commitments and accelerate climate action for the built environment.